Characteristics of rock wool sandwich board
1. Good rigidity: because the rock wool core material is bonded with two layers of steel plates to form a whole and work together, the overall rigidity is much better than the on-site composite plate with rock wool (glass wool) in the profiled plate. After the sandwich panel is fixed with the purlin through the connector, the overall stiffness of the roof is greatly improved and the overall working performance of the roof is strengthened. Rock wool sandwich board is selected, and large purlin distance can be adopted, so 1 / 3 ~ 2 / 3 purlin consumption can be saved.
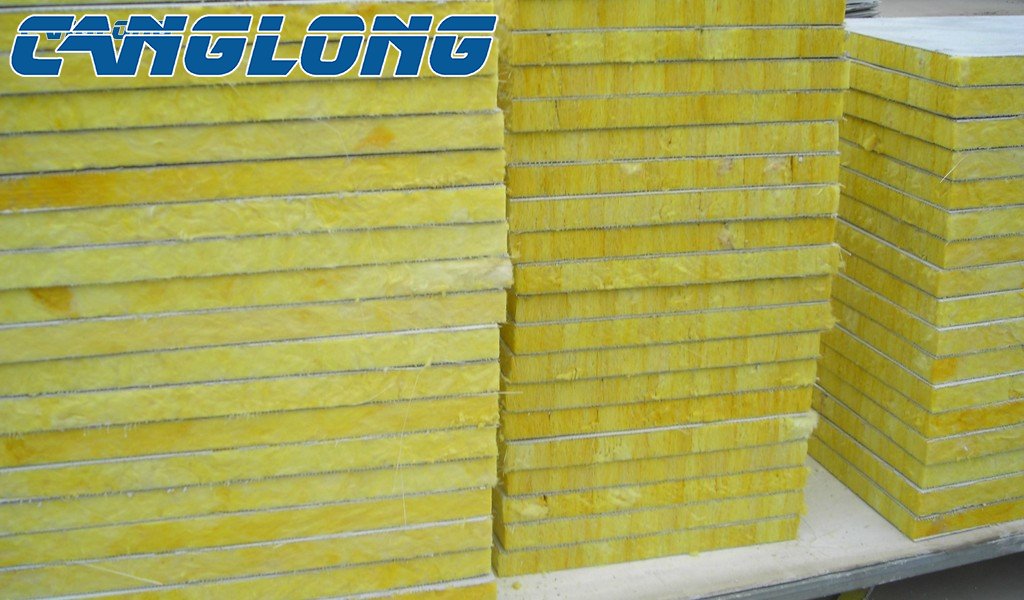
2. Reasonable buckle connection mode: the rock wool roof panel adopts buckle connection mode, which avoids the hidden danger of water leakage at the roof panel joint and saves the amount of accessories.
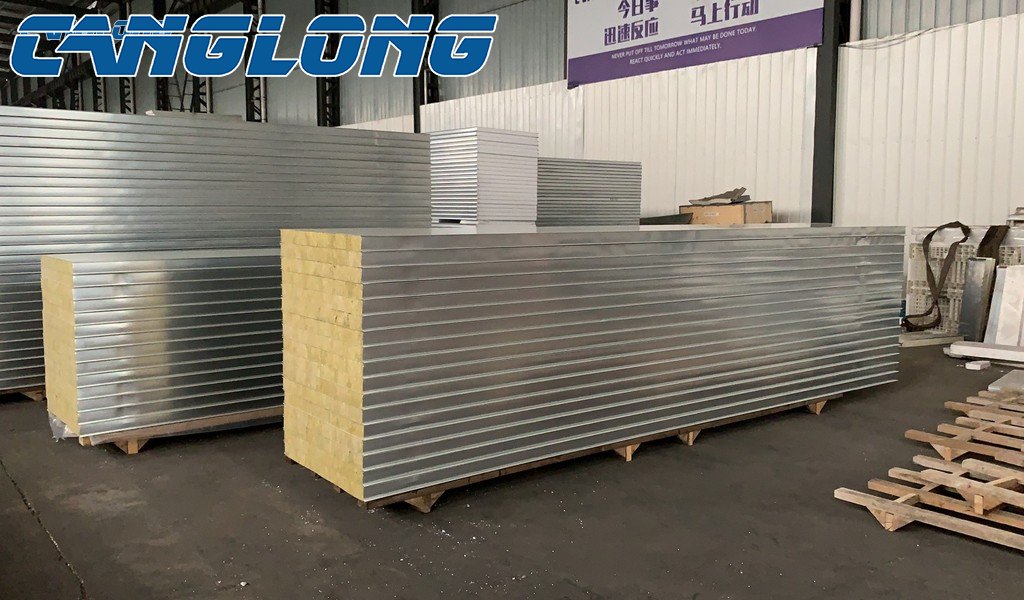
3. The fixing method is firm and reasonable: the rock wool roof panel is fixed with special M6 self tapping screws and purlins, which can effectively resist external forces such as typhoon. The self tapping screw is set at the wave crest on the upper surface of the roof panel, and adopts a special waterproof structure to avoid the weak point of waterproof.
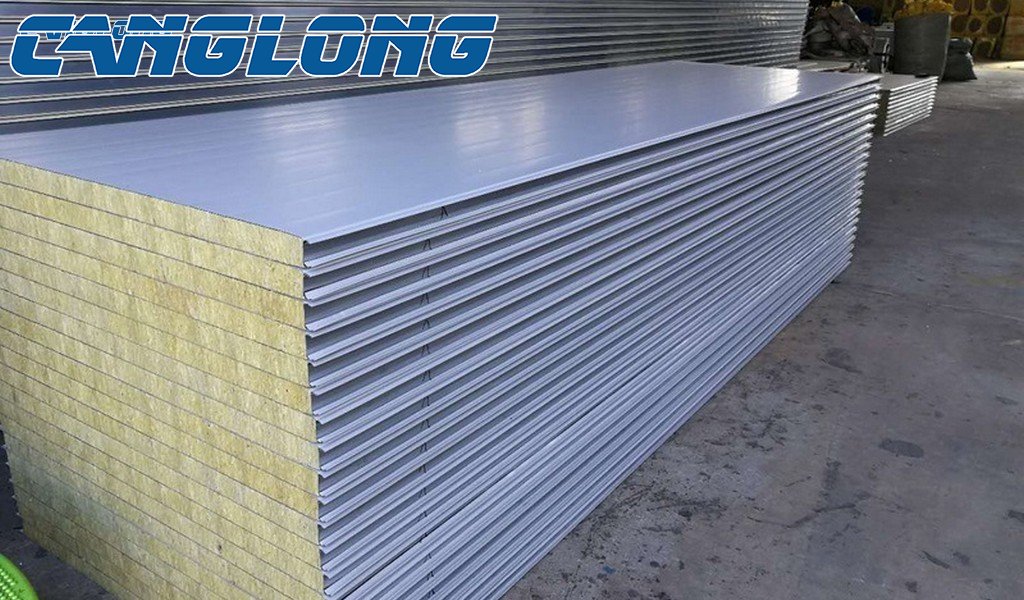
4. Short installation cycle: the rock wool sandwich panel can not only keep the surrounding environment clean and tidy without affecting the normal progress of other processes, but also greatly shorten the installation cycle of the panel. The daily average installation area of the rock wool sandwich panel is 600 ~ 800 m2.
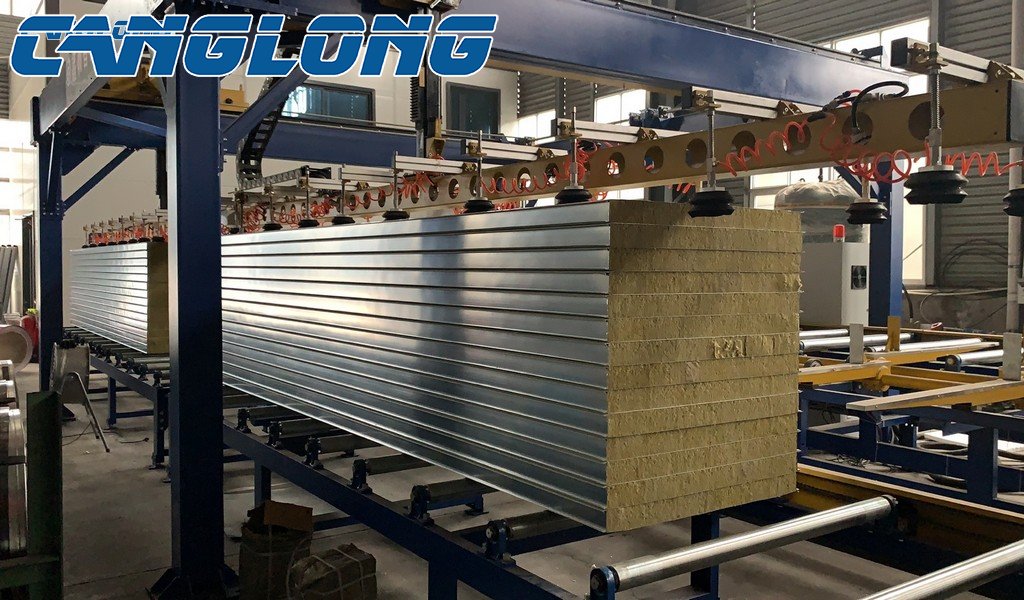
5. Scratch protection: during the production of rock wool sandwich board, polyethylene self-adhesive protective film can be pasted on the surface to avoid scratch or wear on the surface coating of steel plate during transportation and installation.
5. Scratch protection: during the production of rock wool sandwich board, polyethylene self-adhesive protective film can be pasted on the surface to avoid scratch or wear on the surface coating of steel plate during transportation and installation.