Can metal sandwich panels be used as industrial high-temperature protection materials?
As the global industrialization process accelerates, the safety requirements for equipment and buildings in high-temperature working environments are becoming increasingly stringent. Industrial high-temperature protection materials have become the core element to ensure production safety. Among them, metal sandwich panels are creating a technological revolution in the global market with their excellent fire protection, heat insulation and structural stability.
Current status of the global industrial high-temperature protection material market
1. Market size and growth momentum
According to Grand View Research data, the global industrial high-temperature protection material market size will reach US$14.8 billion in 2023, and the compound annual growth rate (CAGR) is expected to reach 6.8% from 2024 to 2030. The core driving factors include:
Industrialization and energy demand: The expansion of the petrochemical, power, and metallurgical industries has driven the demand for high-temperature protection.
Safety regulations have been upgraded: Many countries in Europe, America, and Asia-Pacific have mandatory requirements for industrial buildings to meet Class A fire protection standards.
Material technology innovation: Lightweight and highly fire-resistant sandwich panels are accelerating the replacement of traditional brick-concrete structures.
2. Regional market structure
North America and Europe: occupy 45% of the market share, and strict fire protection regulations and industrial upgrading demand dominate growth.
Asia Pacific: The fastest growth rate (CAGR 8.2%), China, India steel mills, chemical plant new projects surge.
Middle East and Africa: Oil and gas exploration and high-temperature storage facilities construction drive metal sandwich panel procurement.
All-round guard in the field of high-temperature protection of metal sandwich panels
1. Core structure and performance advantages
Metal sandwich panels are composed of galvanized steel plates (outer layer) + fireproof core materials (rock wool, polyurethane, etc.), and their high-temperature protection performance is reflected in:
Fire resistance limit: Class A fireproof sandwich panels can withstand high temperatures of 1200℃ for 1-4 hours to prevent the spread of fire.
Heat insulation and energy saving: The thermal conductivity is as low as 0.022 W/(m·K), reducing heat energy loss by more than 30%.
Corrosion resistance: Fluorocarbon coating process can cope with harsh industrial environments such as acid rain and salt spray.
2. Metal sandwich panels vs. traditional materials
Target | Metal Sandwich Panels | Conventional Concrete | Ordinary Color Steel Plate |
---|---|---|---|
Fire resistance time | 1-4 hours (Grade A) | 2 hours (B-level) | 0.5 hours (without core material) |
Weight | 15-25 kg/m² | 240 kg/m² | 10-15 kg/m² |
Construction period | Reduce by 50% | long | Short (but without insulation) |
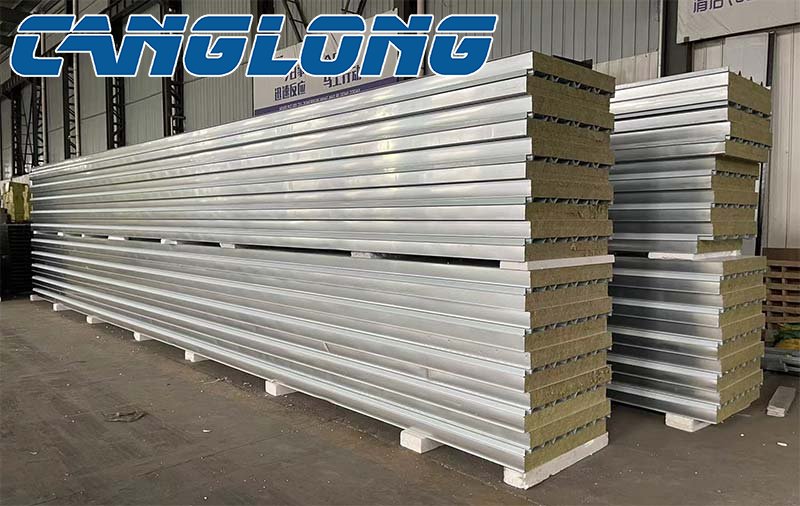
Four core application scenarios of metal sandwich panels
1. Petrochemical industry
Refinery firewall: Use rock wool sandwich panels to isolate high-temperature reaction tanks to reduce the risk of explosion.
Pipeline insulation layer: Cover high-temperature oil pipelines to reduce heat loss.
2. Power and metallurgical industry
Power plant boiler room: Polyurethane sandwich panel roof withstands 800℃ flue gas emissions.
Steel plant operation room: Quick assembly sandwich panel walls protect workers from radiant heat.
3. Warehousing and logistics
High-temperature cargo warehouse: Fireproof sandwich panel warehouses store flammable chemicals and lithium batteries.
Cold chain facilities: Take into account the dual needs of insulation and fire protection.
4. Transportation infrastructure
Tunnel fireproof lining: European high-speed rail tunnels widely use metal sandwich panel systems.
Ship cabin partition: Resistant to the humid and high temperature environment at sea.
Future trends in the global metal sandwich panel market
1. Technological innovation direction
Smart sandwich panels: integrated temperature sensors and self-healing coatings to monitor high temperature risks in real time.
Green materials: bio-based polyurethane core materials and recyclable galvanized steel sheets account for an increased proportion.
2. Regional growth opportunities
Southeast Asia: Manufacturing upgrades in Indonesia and Vietnam have given rise to demand for factory fire protection renovations.
Middle East: Super projects such as NEOM Smart City promote the purchase of Class A fireproof building materials.
3. Industry challenges and countermeasures
Cost pressure: Reduce the price of rock wool core materials (accounting for 40% of the cost) through large-scale production.
Standard differences: Develop multi-national certified products that comply with EU EN 13501 and US ASTM E84.
Key indicators for selecting metal sandwich panel suppliers
Certification qualifications: ISO 9001 quality management system, FM global certification, GB 8624.
Customization capabilities: support non-standard sizes, special-shaped structure design and fast delivery.
Case experience: successful application records in high-risk industries such as chemicals and electricity.
Conclusion
Industrial high temperature protection materials are transforming from passive defense to active safety. Metal sandwich panels have become the preferred solution for global high temperature environment protection with their comprehensive advantages of fire prevention, energy saving and lightweight. Driven by the industrialization of emerging markets and green building policies, the market size of metal sandwich panel is expected to exceed US$22 billion in the next five years. Enterprises need to keep up with material innovation and regional demand to seize the strategic opportunity of this trillion-level track.
Latest News
-
Can metal sandwich panels be used as industrial high-temperature protection materials?
-
Steel structure warehouse: innovative solution for efficient storage and modern storage units
-
Packaged and shipped steel structure garage project for American clients
-
Customized steel structure garage: meeting diverse parking needs